
Stainless steel technique
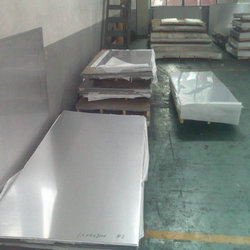

The cooling rate of air cooling is not as fast as that of oil cooling. Therefore, increasing the pressure of the spray chamber, increasing the flow rate, and adopting the inert gas helium and hydrogen with a lower molar mass than nitrogen and argon are the mainstream of the development of vacuum quenching technology. In the late 1970s, the pressure of nitrogen spray cooling was reduced from (1 ~ 2). 10Pa increased to (5 ~ 6)%26times;
10Pa, so that the cooling capacity is close to the oil cooling under normal pressure. In the mid-1980s, ultra-high pressure gas quenching appeared, using (10 ~ 20)%26times; Helium at 10Pa, with cooling capacity equal to or slightly higher than that of oil quenching, has entered industrial use. In the early 1990s, the adoption rate was 26times; Hydrogen at 10Pa, close to water quenching cooling capacity, is still in its infancy. Industrial developed countries have advanced to high pressure. 10. Pa gas quenching is the main body, while the relationship between the vapor pressure (theoretical value) and temperature of some metals produced by Chinese gas quenching is still in the general pressurized gas quenching (2%26times). 10Pa) type stage.
Results vacuum carburizing is a curve of vacuum carburizing and quenching process. After being heated to carburizing temperature in vacuum and kept warm to purify and activate the surface, the rarefied carburized rich gas (see controlled atmosphere heat treatment) was introduced and infiltrated at about 1330Pa(10T0rr) negative pressure, and then the gas was stopped (depressed-pressure) for diffusion. The precision steel tube quenching after carburizing adopts A quenching method, that is, first power failure, nitrogen cooling workpiece to the critical point A,, and below, so that the internal phase change, and then stop gas, open pump, heating up to Ac1, ~ Accm. Gas or oil cooling can be used for quenching.
The latter was austenitized and moved into the anterior chamber, filled with nitrogen to atmospheric pressure and filled with oil. Vacuum carburizing temperature is higher than ordinary gas carburizing, 920 ~ 1040 ℃ is often used as shown in the infiltration and diffusion can be divided into two stages, also can use pulsed ventilation and gas, many sections of the ooze a expansion and white, more effective. Owing to the high temperature, especially surface clean, active, vacuum carburizing layer forming speed is faster than ordinary gas, liquid and solid carburizing and carbonitriding layer to 1 mm, just 5 h at 927 ℃, 1033 ℃ and only 1 h.
The latter was austenitized and moved into the anterior chamber, filled with nitrogen to atmospheric pressure and filled with oil. Vacuum carburizing temperature is higher than ordinary gas carburizing, 920 ~ 1040 ℃ is often used as shown in the infiltration and diffusion can be divided into two stages, also can use pulsed ventilation and gas, many sections of the ooze a expansion and white, more effective. Owing to the high temperature, especially surface clean, active, vacuum carburizing layer forming speed is faster than ordinary gas, liquid and solid carburizing and carbonitriding layer to 1 mm, just 5 h at 927 ℃, 1033 ℃ and only 1 h.